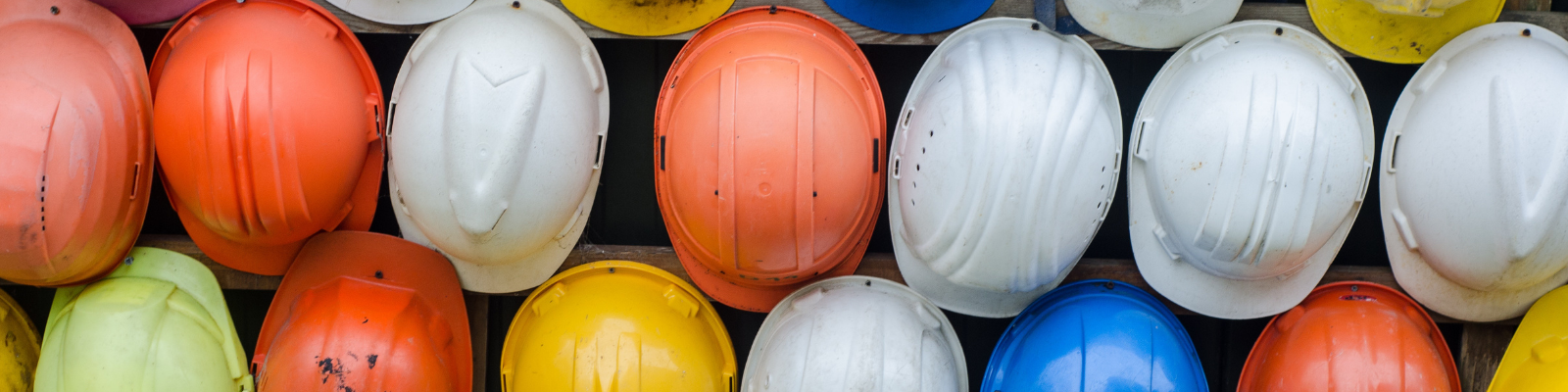
Baler Safety Tips- How to Avoid Injuries When Using a Baler
By following these baler safety tips for operating a baler, you will decrease the risk of baler-related injuries in your company.
Compacting and baling equipment reduce large amounts of solid waste to smaller, more manageable units by utilizing powered rams. These machines are typically used by manufacturing companies to compact and bale large amounts of scrap and waste materials such as paper, cotton, and metals. On the other hand, retail and service industries are using these machines for paper and cardboard boxes which tend to take up a lot of room, just like other waste materials.
Compactors compress the waste material into containers for transport. While baling equipment is designed to compress the material and produce a bale that can be handled and transported as a unit.
It is extremely important to understand that when powerful metal equipment such as balers are used incorrectly, series injuries can occur. Industrial garbage compactors are a very important part of most businesses nowadays however, the majority of the injuries are preventable if these safety tips are followed.
Baler Training is Crucial!
Waste and recycling balers are very easy to use, and they make businesses more efficient by compressing waste into dense compact blocks. However, like any commercial or industrial machinery, balers should only be operated by trained staff and in secure conditions.
Training your staff is key and it is vital that the vendor provides you with thorough instructions on using the machine safely, the appropriate duty of care, how to bale out, how to ready the machine, how to change the banding, and other simple maintenance and cleaning steps.
Safety training and supervision: Never operate a baler without proper safety training and supervision, especially for beginners. It is essential to receive comprehensive training on the operation, controls, and safety protocols associated with balers. Having experienced personnel oversee operations can provide guidance and ensure safe practices are followed.
Visible warning signs: Place clear and visible warning signs next to the waste baler to notify staff of its presence. These signs serve as a constant reminder to exercise caution and be aware of potential hazards associated with the baler.
Proper protective gear: Always wear the appropriate personal protective equipment (PPE) when working with balers. This includes safety glasses, gloves, goggles, earplugs, hard hats, and steel-toed shoes. Each piece of PPE serves a specific purpose in safeguarding against various risks, such as eye injuries from debris, hand injuries from sharp objects, and hearing damage from loud noise.
Power down during jam clearing: When clearing jams in the baler, it is crucial to power down the machine completely. Disconnecting the power supply ensures that the baler will not reactivate accidentally while clearing the jam, preventing potential entanglement or crushing hazards.
Remove key from switch: Operators should remove the key from the baler’s switch when the machine is not in use. This simple step helps prevent unauthorized use or accidental activation, reducing the risk of injuries caused by inadvertent operation.
Pre-use inspection: Before using the baler, conduct a thorough inspection to identify any potential safety issues. Check for loose or damaged parts, malfunctioning controls, or signs of wear and tear. Address any identified issues promptly to maintain the baler’s safe operation.
Clear warning signs and safety decals: Display clear warning signs and safety decals on the baler itself. These visual cues serve as reminders of the specific hazards associated with the machine and the necessary precautions to take while operating it.
Safety Tips for Baling Out
When it comes to baler safety, paying attention to important details can make a significant difference in preventing accidents and ensuring a safe working environment. Here are some additional details to consider when implementing baler safety tips:
Use the correct baler banding: Baler banding plays a crucial role in securing bales and maintaining the integrity of the baler. It is essential to use the appropriate banding that matches your baler’s specifications. Factors to consider include the length, width, breaking strength, material, and quality of the banding. Using the wrong type of banding can lead to band breakage, causing bales to become loose and increasing the risk of injury to workers.
Clear the bale-out area: Before baling out, it is vital to ensure that the area surrounding the baler is clear of any obstructions and personnel. Remove any debris, loose materials, or other objects that may interfere with the baling process. Also, make sure that no one is standing near the baler during operation to prevent accidents caused by entanglement or crushing hazards.
Ensure proper equipment availability: Along with clearing the bale-out area, it is essential to have the necessary equipment readily available nearby. This includes items like pallets or trolleys, which are used to transport and store bales safely. Having these tools within easy reach helps minimize the need for excessive manual lifting, reducing the risk of strain or musculoskeletal injuries for workers.
Baler Safety Tips Conclusion
Prioritizing baler safety is paramount for both workers and employers. It cannot be stressed enough that the improper use of these powerful machines can lead to severe injuries, ranging from crushing to amputation, and in tragic cases, even death. To mitigate these risks, it is crucial to adhere to the safety guidelines provided by the manufacturer. Additionally, investing in proper training for all personnel involved and conducting regular inspections of the equipment are essential steps in minimizing potential hazards associated with balers. By consistently practicing these safety measures, we can significantly decrease the likelihood of accidents and create a safer work environment for everyone involved. Remember, when it comes to baler safety, there is no room for compromise.